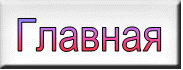

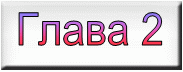
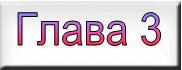
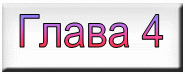
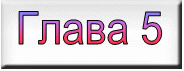
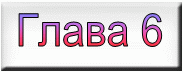
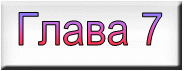
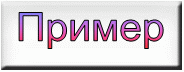
|
ГЛАВА 1. НОРМИРОВАНИЕ ТОЧНОСТИ ЛИНЕЙНЫХ
И УГЛОВЫХ РАЗМЕРОВ
1.1 НОРМИРОВАНИЕ ТОЧНОСТИ ГЛАДКИХ ЦИЛИНДРИЧЕСКИХ СОЕДИНЕНИЙ
1.1.1.Основные понятия и термины
Качество изделий машиностроения зависит от геометрической точности деталей, входящих в них.
Точность есть понятие совокупное, и может быть оценена точностью размеров элементов детали, точностью формы поверхностей и их взаимным расположением, волнистостью и шероховатостью. Нормирование точности размеров осуществляется стандартами Единой системы допусков и посадок (ЕСДП) через систему ГОСТов (Государственных стандартов).
Различают размеры:
номинальный – размер, относительно которого определяются предельные размеры и который служит началом отсчета отклонений, назначается из числа стандартных по ГОСТ 6636.
предельные (наибольший и наименьший) – два предельно допустимых размера, между которыми должен находиться действительный размер годной детали;
действительный – размер, установленный измерением с допускаемой погрешностью.
Принятые обозначения:
D (d) – номинальный размер отверстия (вала);
D(d)max,D(d)min,D(d)e – размер отверстия (вала), наибольший (максимальный), наименьший (минимальный), действительный.
ЕS (es) – верхнее отклонение отверстия (вала);
EI (ei) – нижнее отклонение отверстия (вала);
S, Smax, Smin, Sm – зазор, наибольший (максимальный), наименьший (минимальный), средний соответственно;
N, Nmax, Nmin, Nm – натяг, наибольший (максимальный), наименьший (минимальный), средний соответственно;
TD, Td, TS, TN, TS(N) - допуск отверстия, вала, зазора, натяга, зазора-натяга (в переходной посадке) соответственно;
IT1, IT2 и т.д. – допуск размера по соответствующему квалитету.
Под размером элементов в цилиндрических соединениях понимается диаметр, в плоских – расстояние между параллельными плоскостями по нормали к ним. Числовые значения размеров в машиностроении задаются в миллиметрах (мм).
При обработке каждая деталь приобретает свой действительный размер и может быть оценена как годная, если он находится в интервале предельных размеров, или забракована, если действительный размер вышел за эти границы.
Условие годности деталей может быть выражено следующем неравенством:
D(d)max > D(d)e > D(d)min.
Разность между наибольшим и наименьшим предельными размерами называется допуском размера: Допуск всегда положительная величина.
TD = Dmax – Dmin = |ES–EI| – для отверстия;
Td = dmax – dmin = |es–ei| – для вала.
Допуск является мерой точности размера. Чем меньше допуск, тем меньше допустимое колебание действительных размеров, тем выше точность детали и, как следствие, увеличивается трудоемкость обработки и ее себестоимость. Положение допуска относительно номинального размера определяется отклонениями.
Отклонением размера называется алгебраическая разность между размером (действительным, предельным) и номинальным размером. Отсюда отклонения могут быть действительными или предельными, а предельные – верхним ES (es) и нижним EI (ei):
для отверстия ES = Dmax – D , EI = Dmin – D;
для вала es = dmax – d, ei = dmin – d.
Отклонения могут быть: положительными (со знаком плюс), если
Dmax (dmax), Dmin (dmin) > D(d),
отрицательными (со знаком минус), если Dmax (dmax ), Dmin (dmin) < D(d)
и равными нулю, если Dmax (dmax), Dmin (dmin) = D(d).
При нанесении на чертежах размеров с предельными отклонениями следует соблюдать следующие правила:
верхнее и нижнее отклонения записывают в две строки, располагая верхнее отклонение над нижним
количество знаков при записи верхнего и нижнего отклонений должно быть одинаковым
отклонения, равные нулю, не указывают, например
при симметричном расположении отклонений их значение задают после знака ± цифрами, равными по высоте цифрам номинального размера
Квалитет – совокупность допусков, соответствующих одинаковой степени точности для всех номинальных размеров. Обозначение допуска в квалитете состоит из латинских букв IT (что означает международный допуск) и цифры (цифр) – номера квалитета, например: IT7; IT12 и т.д.
В соединении элементов двух деталей один из них является внутренним (охватывающим), другой – наружным (охватываемым). В ЕСДП всякий наружный элемент называется валом, всякий внутренний элемент – отверстием. Термины «отверстие» и «вал» применяются и к несопрягаемым элементам.
Разность размеров отверстия и вала до сборки определяет характер соединения деталей, т.е. посадку.
Зазор характеризует большую или меньшую свободу относительного перемещения деталей соединения, а натяг – степень сопротивления взаимному смещению деталей в соединении:
S = D – d, если D > d,
N = d – D, если d > D.
1.1.2. Построение единой системы допусков и посадок
Единая система допусков и посадок ЕСДП введена в действие в народном хозяйстве в 1977г. взамен группы государственных стандартов (ОСТ и ГОСТ), образовывающих национальную систему допусков и посадок СССР, условно называемую системой ОСТ.
Общие положения, ряды допусков и основных отклонений для размеров от 0 до 500мм изложены в ГОСТ 25346, который разработан на основе требований Международной системы допусков и посадок ИСО.
Рекомендации по замене допусков и посадок системы ОСТ полями допусков ЕСДП даны в справочной литературе
В ЕСДП предусмотрено 20 квалитетов: 01; 0; 1; 2; 3; ...; 18. Точность убывает от IT01 к IT18. Квалитеты IT01; IT0 и IT1 предназначены для оценки точности плоскопараллельных концевых мер длины, IT2, IT3 и IT4 – для гладких калибров пробок и скоб; IT5 ... IT17 – производственные квалитеты для металлических деталей, в которых IT4...IT6 используются для высокоточных деталей; IT7, IT8 применяются для деталей ответственных соединений в машиностроении и приборостроении, а IT9, IT10 – для деталей неответственных соединений (сельскохозяйственное машиностроение, грузовой автомобиль, подъемно-транспортное оборудование и т.д.). Квалитеты IT11, IT12 – используются также для неответственных соединений, в которых требуются большие зазоры, при значительных температурных перепадах, при работе в запыленных условиях; IT12...IT17 назначаются для размеров металлических деталей с неуказанными допусками, т.е. для размеров не образующих соединения; IT18 предназначен для деталей из пластмасс.
Допуски в квалитетах IT5...IT17 вычисляются для каждого интервала номинальных размеров по зависимости: ITn = аn i,
где an – безразмерный коэффициент (число единиц допуска), установленный для каждого n-го квалитета и являющийся постоянным числом для данного квалитета; n – номер квалитета; i – единица допуска, являющаяся функцией номинального размера (гиперболическая зависимость), (мкм).
Начиная с 5-го квалитета допуски при переходе к следующему более грубому квалитету возрастают по геометрической прогрессии со знаменателем ?=1,6, а, начиная с 6-го квалитета (для IT6 a =10) через каждые пять квалитетов – увеличиваются в 10 раз, например , IT6 = 10i, то IT11=10IT6 = 100i.
Для полей допусков, у которых основным является верхнее отклонение, нижнее отклонение отрицательное вычисляется по формулам:
для вала ei = es – IT (основные отклонения a... h),
для отверстия EI = ES – IT (основные отклонения J ... ZC).
Если основное отклонение – нижнее, то верхнее отклонение вычисляется по формулам:
для вала es = ei + IT (основные отклонения j... zc);
для отверстия ES = EI + IT (основные отклонения А... Н).
1.1.3. Неуказанные предельные отклонения размеров
Предельные отклонения номинальных размеров низкой точности (размеры несопрягаемых поверхностей, неответственных соединений), не приведенные непосредственно после них на чертеже, а оговоренные общей записью в технических требованиях, называются неуказанными предельными отклонениями.
Для линейных размеров, кроме радиусов закруглений и фасок, неуказанные предельные отклонения могут назначаться по квалитетам или по классам точности: точный (t1), средний (t2), грубый (t3) и очень грубый (t4), которые установлены в ГОСТ 25670 (см. табл.1.5). Предельные отклонения в них получены грубым округлением числовых значений по квалитетам IT12, IT14, IT16, IT17 при укрупненных интервалах номинальных размеров.
Неуказанные предельные отклонения допускается назначать односторонними « в тело» материала (для валов от нуля в минус: – t,(h); для отверстий – от нуля в плюс + t,(H)), а для длин, глубин, межосевых расстояний, радиусов симметричными ± t/2,(±IT/2).
Классификация конструктивных элементов деталей по трем группам (валы, отверстия и элементы, не относящиеся к валам и отверстиям) показана на рис.1.3.
Согласно ГОСТ 25670 допускается четыре варианта назначения неуказанных предельных отклонений линейных размеров, в каждом из которых может быть оговорен любой уровень точности, предусмотренный квалитетами или классами точности для неуказанных отклонений. Выбор варианта общей записи в технических требованиях чертежа зависит от конструктивных и технологических условий машиностроительного производства. Предпочтение следует отдать заданию неуказанных предельных отклонений односторонними «в тело», так как при этом способе задания гарантируется соблюдение предписанных зазоров, свободный проход деталей в других деталях при сборке, при одинаковых номинальных размерах наблюдается снижение массы деталей и экономия материала. Например, в технических требованиях к чертежу может быть сделана одна из следующих записей (относится к классу точности – средний):
+ t2; - t2; ? t2/2;
H14; h14; ?t2/2;
H14; h14; ?IT14/2.
В приборостроении, авиастроении наиболее часто используется для назначения неуказанных предельных отклонений точный класс (t1) или IT12. Для радиусов закруглений и фасок в ГОСТ 25670 установлено два ряда особых (более грубых) предельных отклонений. В общей записи о неуказанных отклонениях применение ряда отдельно не оговаривается, а связывается с квалитетом или классом точности, предписанным в этой записи для других линейных размеров.
Подобным образом регламентируются неуказанные предельные отклонения углов.
1.2. РАСЧЕТ ПОСАДОК И НАЗНАЧЕНИЕ ПОЛЕЙ ДОПУСКОВ
Посадки в системе отверстия и в системе вала
Конструктор назначает посадки в виде определенного сочетания полей допусков отверстия и вала, причем номинальный размер отверстия и вала является общим (одинаковым) D=d и называется номинальным размером соединения. Существуют три типа посадок: с зазором, натягом и переходные, которые могут быть назначены в системе отверстия (СH) или в системе вала (Сh). Выбор системы диктуется конструктивными, технологическими или экономическими соображениями.
В системе отверстия посадки осуществляются между основным с отверстием с основным отклонением H и валами с различными основными отклонениями (a...zc).
В системе вала посадки осуществляются между основным валом с основным отклонением h и отверстиями с различными основными отклонениями (A...ZC).
Из двух систем предпочтительной является СH, так как обработать точное отверстие дороже, чем точный вал, а для производства разных по точности отверстий в системе Сh требуется множество мерных режущих инструментов (сверл, зенкеров, разверток, протяжек и т.д.) и средств контроля.
Система вала применяется реже, в экономически обоснованных случаях:
на валах, изготовленных из калиброванного холоднотянутого прутка без обработки резанием посадочных поверхностей;
в соединении длинного участка вала одного номинального размера с отверстиями в нескольких деталях с различными характеристиками посадки;
в соединениях стандартных деталей и узлов, выполненных в системе вала (наружное кольцо подшипника, шпонка по ширине и др.)[4,12].
Посадки могут быть выполнены с зазором -S, натягом- N и переходными- S(N).
Различают Smin, Smax, Sm и Nmin, Nmax, Nm, которые количественно оценивают посадку и подсчитываются по формулам:
Smin = Dmin – dmax = |EI – es|,
Smax = Dmax – dmin = |ES – ei|,
Sm = (Smax + Smin)/2 = Dm ? dm.
Nmin = dmin – Dmax = |ei – ES|,
Nmax = dmax – Dmin = |es – EI|,
Nm = (Nmax + Nmin)/2 = dm – Dm.
Допуск посадки с зазором TS = Smax – Smin = TD + Td.
Значение Smin иногда называют гарантированным зазором. К посадкам с зазором относятся посадки H/h в различных квалитетах, в которых нижняя граница поля допуска отверстия совпадает с верхней границей поля допуска вала. Для них Smin=0.
В посадке с натягом поле допуска отверстия расположено под полем допуска вала (рис.1.5), т.е. действительный размер вала до сборки больше действительного размера отверстия. Требуется применение силового или теплового воздействия (нагрев втулки или охлаждение вала).
Допуск посадки с натягом TN = Nmax – Nmin = Td + TD, где Nmin – гарантированный натяг.
Переходной посадкой называется посадка, в которой при сборке возможно получение как зазора, так и натяга. Эти посадки обеспечивают точное центрирование (совпадение осей) втулки относительно оси вала. В такой посадке поля допусков отверстия и вала частично или полностью перекрывают друг друга
Переходные посадки характеризуются наибольшими значениями натяга Nmax и зазора Smax.
Допуск переходной посадки ТS(N) = TD + Td = Nmax + Smax.
В переходной посадке средний натяг (зазор) рассчитывается по формуле:
Nm(Sm)= dm – Dm (Dm ? dm ) = (Nmax ? Smax )/2. Результат со знаком минус будет означать, что среднее значение для посадки соответствует Sm.
Допуск посадки всегда равен сумме допусков отверстия и вала
Кроме основных посадок могут быть образованы посадки, в которых поля допусков отверстия и вала принадлежат разным системам: отверстие из системы вала, вал из системы отверстия. Такие посадки называются внесистемными или комбинированными. Комбинированной также будет называться посадка, если поля допусков отверстия и вала будут принадлежать одной системе, но отличаться по точности отверстия по отношению к валу на один, два квалитета. Назначаться они могут в случае, если поле допуска одной из сопрягаемых деталей определяется соединением с третьей, чаще всего стандартной деталью или узлом. Например, в соединении гладкого вала с распорной втулкой, поле допуска вала (k6) зависит от характера его соединения с подшипником (L0/k6).Тогда для образования зазора, обеспечивающего легкость сборки в соединении вал – распорная втулка, на отверстие во втулке требуется назначить, например, поле допуска F8. Таким образом, получится посадка F8/k6 – внесистемная (основное отклонение отверстия–F из системы вала, основное отклонение вала – k из системы отверстия) и комбинированная по квалитетам–IT8 для отверстия, IT6 – для вала
Подбор посадок методом подобия
Метод подобия при назначении посадок используется при наличии большого справочного материала по применению посадок в конструкциях.
При совпадении конструктивных и эксплутационных показателей проектируемого и аналогичного изделия (рекомендуемого по справочнику) производится выбор посадки
Аналоговыми будут считаться конструкции, совпадающие с проектируемыми по характеру соединения (типу посадки) ¬с зазором, натягом или переходная, по системе посадки (СН или Сh), по точности изделия (машины, механизма), а также по экономической точности обработки деталей сопряжения в нормальных производственных условиях.
Посадки с зазором могут назначаться в квалитетах с 5-го по 12-й.
Посадки с натягом и переходные применяются в точных квалитетах с 5-го по 8-й, при этом квалитет отверстия рекомендуется принимать грубее квалитета вала на один.
При выборе посадок из стандартных полей допусков необходимо использовать посадки предпочтительно применения.
По рассматриваемой конструкции выбирается система посадки
,определяется тип посадки (с зазором, натягом или переходные) и вид сопряжения (скользящая, ходовая, прессовая и т.д.).
Выбирается квалитет точности, учитывая условия эксплуатации данного
соединения.
Определяются предельные отклонения сопрягаемых деталей, строится схема расположения полей допусков, рассчитываются предельные и среднее значения зазоров или натягов и допуск посадки. Указываются посадки на сборочном чертеже, а поля допусков на чертежах деталей, входящих в изделие (в смешанном виде).
1.3. ДОПУСКИ РАЗМЕРОВ, ВХОДЯЩИХ В РАЗМЕРНЫЕ ЦЕПИ
1.3.1. Основные понятия и определения
Размерная цепь - совокупность взаимосвязанных линейных (или угловых) размеров, образующих замкнутый контур и определяющих собой взаимное положение деталей в механизме или поверхностей и осей в детали.
По техническим функциям размерные цепи можно разделить на конструкторские (сборочные), технологические (операционные) и измерительные. Здесь рассматриваются только конструкторские размерные цепи. Простейшей размерной цепью будет соединение вала с отверстием, так как эта размерная цепь содержит наименьшее число размеров – три и размеры расположены параллельно: вал - зазор (натяг) - отверстие.
Наиболее общий случай представляют пространственные размерные цепи. Однако всякую пространственную размерную цепь путём проектирования на плоскости, а затем и на оси координат можно заменить размерными цепями с параллельно расположенными размерами.
Таким образом, решение как пространственной, так и плоской размерной цепи в конечном счёте сводится к решению линейной размерной цепи с параллельно расположенными размерами (звеньями).
Размерная цепь состоит из замыкающего (исходного) и составляющих размеров (звеньев).
Замыкающий размер А? – это размер размерной цепи, получающийся последним в результате сборки узла. В конструкторской размерной цепи замыкающим размером является либо зазор, либо натяг, либо величина смещения одной детали относительно других в процессе функционирования механизма (здесь замыкающий размер называют исходным).
Исходное звено определяет технические требования к точности изделия и правильное функционирование механизма, поэтому конструктор прежде всего устанавливает его допустимые отклонения.
Составляющими размерами (звеньями) размерной цепи являются размеры, изменение которых приводит к изменению размера замыкающего звена.
В зависимости от влияния составляющих размеров на замыкающий размер составляющие размеры подразделяются на увеличивающие и уменьшающие.
Увеличивающими размерами называются такие размеры (звенья), увеличение которых приводит к увеличению замыкающего звена.
Уменьшающими размерами называются такие размеры (звенья), увеличение которых приводит к уменьшению замыкающего звена.
Размерные цепи, выявленные на сборочном чертеже, изображают отдельно в виде схем. Размеры, входящие в размерные цепи, обозначают буквами русского алфавита. Замыкающий (исходный) размер принято отмечать индексом , а составляющие – индексами 1,2,3,...,n, например, и т.д. – замыкающие звенья, и т.д., и т.д. – составляющие звенья.
В сложных размерных цепях увеличивающие и уменьшающие звенья определяют методом замкнутого потока. Для этого над замыкающим размером на схеме размерной цепи пунктиром ставится левонаправленная стрелка , и вся цепь обходится против часовой стрелки, образуя замкнутый контур. Все звенья, направление стрелок над которыми совпадут с замыкающим, будут уменьшающими, а звенья с противоположно направленными стрелками – будут увеличивающими.
1.3.2 Порядок расчёта размерной цепи по методу «максимум - минимум»
• Составить условное безмасштабное изображение размерной цепи (схему) по заданному варианту.
• Определить увеличивающие и уменьшающие размеры методом замкнутого потока, начиная обозначение всегда с простановки у замыкающего звена пунктиром левонаправленной стрелки.
• Рассчитать номинальный размер А? замыкающего звена по формуле:
А? = ?Аi - ?Аj
где i и j - увеличивающие и уменьшающие размеров в размерной цепи соответственно
• Рассчитать верхние ES? и нижние EI? предельные отклонения и допуск T? замыкающего размера (звена) по формулам:
ES?=A?max-A?; EI?=A?min-A?; T?=A?max-A?min=ES?-EI?
• Определить средний квалитет составляющих размеров (звеньев) размерной цепи по среднему числу единиц допуска , приходящемуся на одно звено, исключая стандартизованные (подшипники качения и т.д.), если таковые имеются, по формуле
a = T*1000/?i
где T – допуск замыкающего звена за вычетом суммы допусков стандартизованных размеров (при их наличии), мм; ij – значение единицы допуска
• Назначить для составляющих размеров (звеньев) конкретный квалитет по расчётному значению - a.
• Найти стандартные поля допусков по ГОСТ 25347 на составляющие размры цепи по установленным для них квалитетам. Знаки отклонений следует указывать так, чтобы допуск по возможности был направлен «в тело» детали (см. рис. 1.3):
1) для размеров охватывающих (внутренних) поверхностей отклонения назначать в плюс, как для основного отверстия (Н);
2) для размеров охватываемых (наружных) поверхностей отклонения назначать в минус, как для основного вала (h);
3) для остальных размеров – симметричные отклонения .
Определить расчётное поле допуска замыкающего звена
и сравнить его с заданной величиной допуска.
Если расхождение значительное, то необходимо сменить точность одного-двух размеров в размерной цепи, причем допуски на эти размеры должны остаться стандартными.
Проверить соответствие предельных отклонений размеров требованиям замыкающего звена.
Для отличия заданных величин от расчётных последние должны быть помечены индексом в виде штриха.
1.4. НОРМИРОВАНИЕ ТОЧНОСТИ УГЛОВЫХ РАЗМЕРОВ
Единицами измерения углов могут быть следующие величины:
– международные единицы - радиан и стерадиан (ГОСТ 8.417);
– практическая единица в градусной мере (градус, минута, секунда);
– метрические единицы (мкм; мм), учитывающие соотношение угловых и линейных единиц на заданной длине измерения.
Нормальные ряды углов общего назначения даны в ГОСТ 8908.
Допуск угла обозначается – АТ. Установлено 17 степеней точности в порядке уменьшения точности: 1, . . . ,17.
Степени точности АТ1 ? АТ5 применяются для углов измерительных средств и калибров и требуют тонкого шлифования с последующей доводкой.
Степени точности АТ4 ? АТ12 используются для сопрягаемых углов и конусов, остальные – для углов с неуказанными допусками.
Допуски углов назначаются в зависимости от номинальной длины меньшей стороны угла, так как чем меньше длина, тем труднее изготовить и измерить угол (рис. 1.8.):
- АТ d– в угловых единицах рад; мкрад;
- АТ? d– округлённое значение допуска угла в градусной мере;
- АTh; АТD – допуски угла в метрической системе единиц (мкм).
- АТh – длина противолежащего отрезка на перпендикуляре к стороне угла на расстояние L от вершины угла (рис. 1.8, а и рис. 1.8, в);
- АТD – разность диаметров в двух сечениях конуса на расстояние L между ними.
Различают три основных типа расположения поля допуска относительно номинального угла: плюсовое (+АТ*) ; минусовое (-АТ*); симметричное (АТd/2).
На чертежах указываются числовое значение допуска угла с учётом знака, единица измерения, а также координаты расположения угла относительно оси или плоскости детали.
Конусность С определяется по формуле С=(D - d)/L=2tg(*/2).
Для малых углов (С?1:3): АTD * ATh.
Связь между допусками углов в угловых и линейных единицах определяется по формуле: АТh=10-3АT*L , где ATh в мкм; АТd – мкрад; L – мм
Для конусов с конусностью больше, чем 1:3, значение АТD определяется по формуле. АТD = АТh/cos(*/2), где ? – номинальный угол конуса.
|